ZJ50/70DB all-digital driller control system has truly realized all-digital intelligent control of drilling rigs, reduced the number and simplified the mechanical structure of instruments in the driller room, and filled the gap in the technical field of China.
The new type integrated driller control system is a device newly developed by our company for oil drilling, which is based on automation control, computer and field bus technologies for logic control, protection and monitoring of winch, rotary table, top drive, sludge pump, iron roughneck, tube drawbench, automatic catwalk, power rat-hole, air operated slips and other drilling equipments.
Composed of control units at the management, central and field levels, this system has realized the all-digital, intelligent, networked, visual and highly integrated monitoring, fault diagnosis, parameter modification, diagnosis, storage, recording and other operations of modern drilling rigs through touch screen, industrial personal computer (IPC) and remote computer.
Appearance of new type driller’s station
The monitor screen (20”) in front of the driller’s station mainly replaces the original weight indicator, pump pressure meter, brake manometer (pressure of safety caliper, left caliper and right caliper), air supply pressure gauge, oil manometer (oil pressure of rotary table and winch), which is coupled, in a unified manner, with the pipeline below the control cabinet in the driller control room through piezometer tube or copper tube for connection with various signal sensors; meanwhile, sensors in this part converts liquid-gas signals into electric signals for input in PLC of the electrical control system, display on the screen after computation in the PLC, and finally for alarm and brake control in the event of fault.
Touch screens on the left and right sides are 10” TFT displays of Simens TP270 series. The two screens back up each other, among which, one is used as the electrical control panel, while the other as display of electrical parameters. They enable start/stop and speed control, and real-time state inspection of winch, rotary table, sludge pump and other devices. Boxes in this part are arranged for positive pressure explosion proof, and communication lines of touch screens, power and switching lines are connected with the plugboard in the electrical control cabinet through seal joints or plug connectors.
The new type all-digital driller control system can be used for control, monitoring, data storage and management of all equipments in the well site, including monitoring over operating parameters and status, fault alarm and ground detection of electrical control equipments (winch/rotary table/top drive/sludge pump/automatic driller/iron roughneck/automatic tube drawbench/automatic catwalk/power rat-hole/air operated slips), drilling instruments and auxiliary control equipments. In addition, monitor screen of the IPC is designed with help menus of fault alarm, through which, the platform electrician can find out the fault causes and the corresponding solutions according to the current fault values.
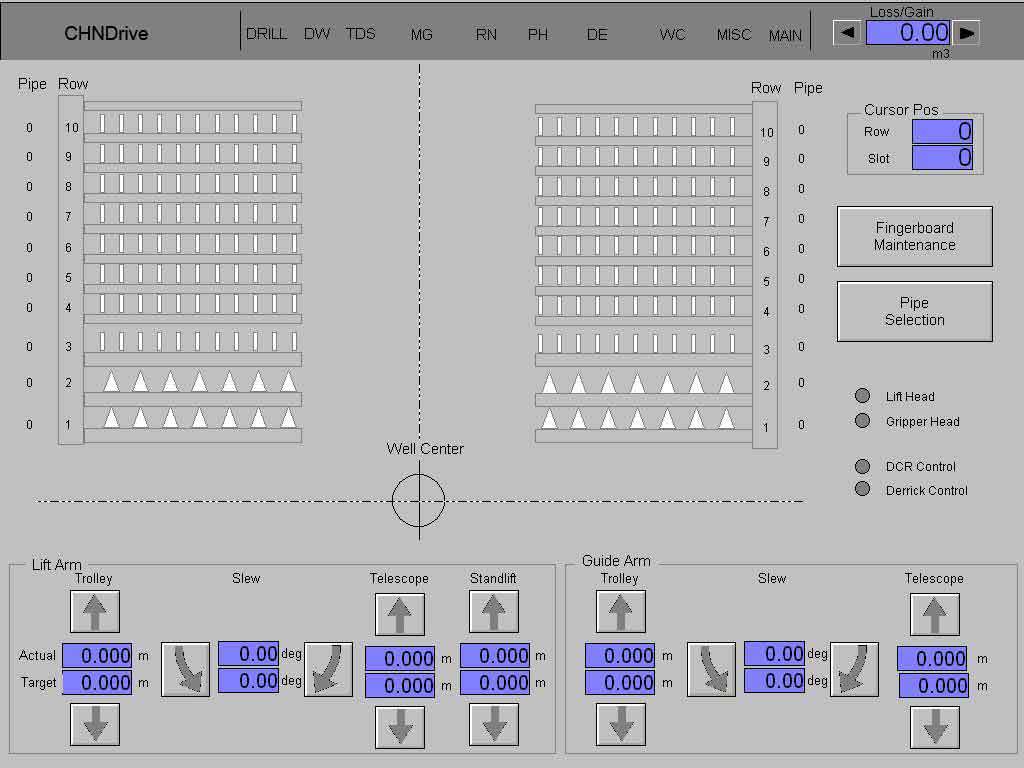